在柔性屏量產進程中,“10 萬次循環彎折” 是衡量產品可靠性的關鍵指標,而 U 錯動彎折試驗機與 “10 萬次循環可視化技術” 的深度融合,正成為柔性屏量產追溯體系的核心支撐工具,為產業鏈質量管控提供全周期數據保障。

傳統彎折測試雖能記錄循環次數與最終結果,但無法捕捉過程中的微觀變化,一旦出現批量質量問題,難以追溯具體失效節點。而搭載 “10 萬次循環可視化技術” 的 U 錯動彎折試驗機,通過集成高速工業相機與紅外熱成像模塊,可實時記錄柔性屏在每一次彎折中的像素點亮狀態、應力集中區域溫度變化及微觀裂紋萌生過程,形成完整的動態數據庫。 該技術的核心優勢體現在 “全程可追溯”。設備在 10 萬次循環測試中,每 500 次自動生成一幀高清影像,同步標記異常參數 —— 當屏體某區域溫度驟升 0.5℃以上時,系統自動觸發局部掃描,精度可達 0.01mm2,精準定位潛在缺陷。測試結束后,生成的可視化報告包含時間軸、溫度場分布、像素失效圖譜等多維數據,工程師可回溯任意循環節點的狀態,快速分析失效機理。

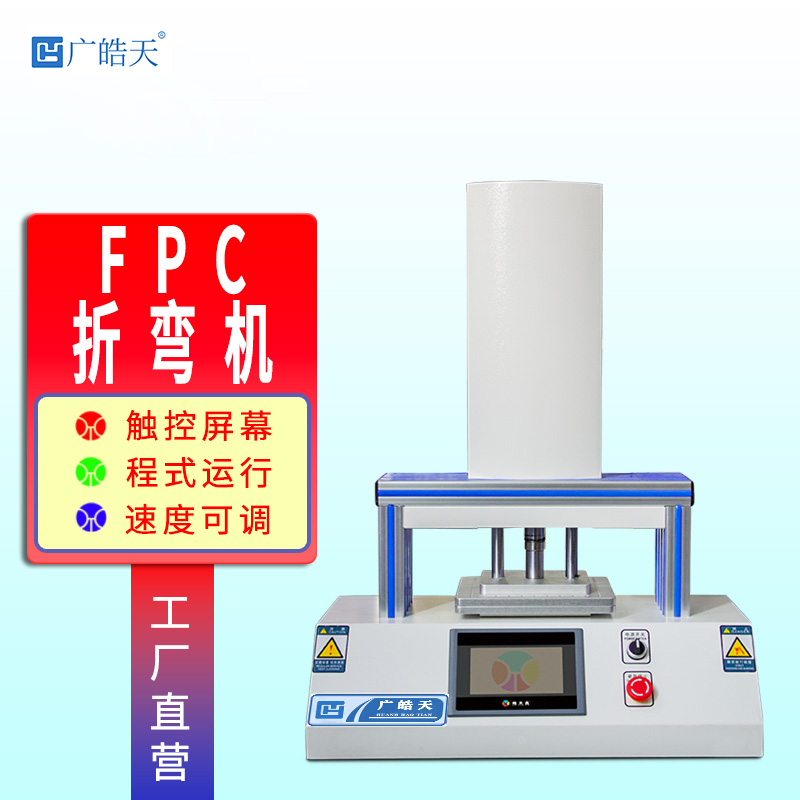
對于量產追溯而言,該技術實現了 “個體 - 批次 - 工藝” 的三級關聯。每片測試屏體的二維碼與可視化數據庫綁定,掃碼即可調閱全周期測試數據;同一批次產品的測試數據通過算法生成質量波動曲線,當某批次合格率低于 99.5% 時,自動關聯生產環節的鍍膜參數、切割精度等工藝數據,助力快速定位問題根源。京東合肥基地應用該系統后,柔性屏量產不良率追溯時間從原來的 48 小時縮短至 2 小時。
技術落地中,設備攻克了 “高頻振動下成像穩定” 難題 —— 采用磁懸浮減震平臺,將相機抖動控制在 ±0.001mm,確保 10 萬次循環中影像的一致性。同時,開發的 AI 分析模型可自動識別 98% 以上的常見缺陷,將人工判讀時間減少 60%。
業內專家指出,該技術使柔性屏從 “達標即合格” 升級為 “過程可追溯”,推動行業從經驗管控轉向數據驅動。隨著折疊屏手機等產品進入億級量產時代,U 錯動彎折試驗機搭載的 “10 萬次循環可視化技術”,正成為產業鏈保障品質、提升效率的關鍵基礎設施,為柔性顯示技術規模化應用筑牢質量防線。
版權與免責聲明:
凡本網注明"來源:儀表網"的所有作品,版權均屬于儀表網,未經本網授權不得轉載、摘編或利用其它方式使用上述作品。已經本網授權使用作品的,應在授權范圍內使用,并注明"來源:儀表網"。違反上述聲明者,本網將追究其相關法律責任。
本網轉載并注明自其它來源的作品,目的在于傳遞更多信息,并不代表本網贊同其觀點或證實其內容的真實性,不承擔此類作品侵權行為的直接責任及連帶責任。其他媒體、網站或個人從本網轉載時,必須保留本網注明的作品來源,并自負版權等法律責任。
如涉及作品內容、版權等問題,請在作品發表之日起一周內與本網聯系,否則視為放棄相關權利。
合作、投稿、轉載授權等相關事宜,請聯系本網。聯系電話:0571-87759945,QQ:1103027433。